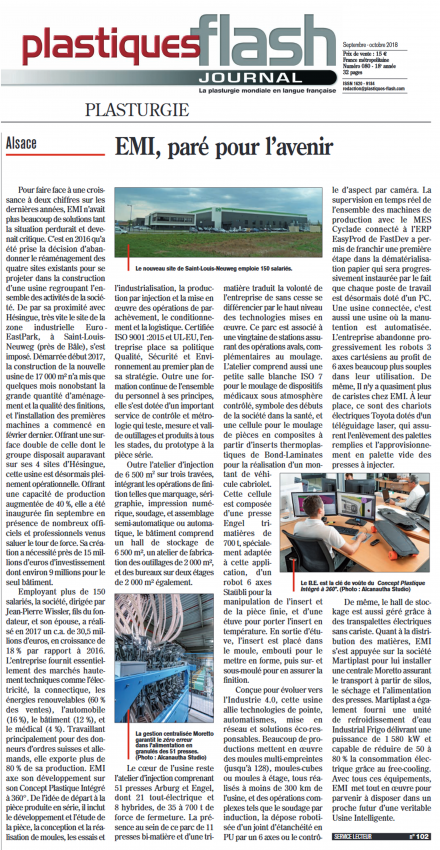
EMI, paré pour l’avenir
Par la rédaction, le
Pour faire face à une croissance à deux chiffres sur les dernières années, EMI n’avait plus beaucoup de solutions tant la situation perdurait et devenait critique. C’est en 2016 qu’a été prise la décision d’abandonner le réaménagement des quatre sites existants pour se projeter dans la construction d’une usine regroupant l’ensemble des activités de la société. De par sa proximité avec Hésingue, très vite le site de la zone industrielle Euro -East Park, à Saint-Louis-Neuweg (près de Bâle), s’est imposé. Démarrée début 2017, la construction de la nouvelle usine de 17 000 m² n’a mis que quelques mois nonobstant la grande quantité d’aménagement et la qualité des finitions, et l’installation des premières machines a commencé en février dernier. Offrant une surface double de celle dont le groupe disposait auparavant sur ses 4 sites d’Hésingue, cette usine est désormais pleinement opérationnelle. Offrant une capacité de production augmentée de 40 %, elle a été inaugurée fin septembre en présence de nombreux officiels et professionnels venus saluer le tour de force. Sa création a nécessité près de 15 millions d’euros d’investissement dont environ 9 millions pour le seul bâtiment.
Employant plus de 150 salariés, la société, dirigée par Jean-Pierre Wissler, fils du fondateur, et son épouse, a réalisé en 2017 un c.a. de 30,5 millions d’euros, en croissance de18 % par rapport à 2016.L’entreprise fournit essentiellement des marchés hautement techniques comme l’électricité, la connectique, les énergies renouvelables (60% des ventes), l’automobile (16 %), le bâtiment (12 %), et le médical (4 %). Travaillant principalement pour des donneurs d’ordres suisses et allemands, elle exporte plus de 80 % de sa production. EMI axe son développement sur son Concept Plastique Intégré à 360°. De l’idée de départ à la pièce produite en série, il inclut le développement et l’étude de la pièce, la conception et la réalisation de moules, les essais et l’industrialisation, la production par injection et la mise en œuvre des opérations de parachèvement, le conditionnement et la logistique. Certifiée ISO 9001 :2015 et UL-EU, l’entreprise place sa politique Qualité, Sécurité et Environnement au premier plan de sa stratégie. Outre une formation continue de l’ensemble du personnel à ses principes, elle s’est dotée d’un important service de contrôle et métrologie qui teste, mesure et valide outillages et produits à tous les stades, du prototype à la pièce série.
Outre l’atelier d’injection de 6 500 m2sur trois travées, intégrant les opérations de finition telles que marquage, sérigraphie, impression numérique, soudage, et assemblage semi-automatique ou automatique, le bâtiment comprend un hall de stockage de 6 500 m², un atelier de fabrication des outillages de 2000m², et des bureaux sur deux étages de 2 000 m² également.
Le cœur de l’usine reste l’atelier d’injection comprenant51 presses Arburg et Engel, dont 21 tout-électrique et8 hybrides, de 35 à 700 t de force de fermeture. La présence au sein de ce parc de 11presses bi-matière et d’une tri-matière traduit la volonté de l’entreprise de sans cesse se différencier par le haut niveau des technologies mises en œuvre. Ce parc est associé à une vingtaine de stations assurant des opérations avals, complémentaires au moulage. L’atelier comprend aussi une petite salle blanche ISO 7pourle moulage de dispositifs médicaux sous atmosphère contrôlé, symbole des débuts de la société dans la santé, et une cellule pour le moulage de pièces en composites à partir d’inserts thermoplastiques de Bond-Laminates pour la réalisation d’un montant de véhicule cabriolet. Cette cellule est composée d’une presse Engel tri-matières de700 t, spécialement adaptée à cette application, d’un robot 6 axes Staübli pour la manipulation de l’insert et de la pièce finie, et d’une étuve pour porter l’insert en température. En sortie d’étuve, l’insert est placé dans le moule, embouti pour le mettre en forme, puis sur- et sous-moulé pour en assurer la finition.
Conçue pour évoluer vers l’Industrie 4.0, cette usine allie technologies de pointe, automatismes, mise en réseau et solutions écoresponsables. Beaucoup de productions mettent en œuvre des moules multi-empreintes (jusqu’à 128), moules-cube soumoules à étage, tous réalisés à moins de 300 km de l’usine, et des opérations complexes tels que le soudage par induction, la dépose robotisée d’un joint d’étanchéité en PU par un 6axes ou le contrôle d’aspect par caméra. La supervision en temps réel de l’ensemble des machines de production avec le MES Cyclade connecté à l’ERPEasy Prod de FastDev a permis de franchir une première étape dans la dématérialisation papier qui sera progressivement instaurée par le fait que chaque poste de travail est désormais doté d’un PC. Une usine connectée, c’est aussi une usine où la manutention est automatisée. L’entreprise abandonne progressivement les robots 3axes cartésiens au profit de6 axes beaucoup plus souples dans leur utilisation. De même, Il n’y a quasiment plus de caristes chez EMI. À leur place, ce sont des chariots électriques Toyota dotés d’un téléguidage laser, qui assurent l’enlèvement des palettes remplies et l’approvisionnement en palette vide des presses à injecter. De même, le hall de stockage est aussi géré grâce à des transpalettes électriques sans cariste. Quant à la distribution des matières, EMI s’est appuyée sur la société Martiplast pour lui installer une centrale Moretto assurant le transport à partir de silos, le séchage et l’alimentation des presses. Martiplast a également fourni une unité de refroidissement d’eau Industrial Frigo délivrant une puissance de 1 580 kW et capable de réduire de 50 à80 % la consommation électrique grâce au free-cooling. Avec tous ces équipements, EMI met tout en œuvre pour parvenir à disposer dans un proche futur d’une véritable Usine Intelligente.
Source : Plastiques flash journal >> Plasturgie >> p.6 >> Septembre-octobre 2018
Retrouvez cet article